Highest R-Value Per Dollar, Most Cost-Effective Insulation Solutions
Expanded polystyrene (EPS) is a premier material for protecting homes, foods and sensitive materials because of its cost-effective, efficient insulation qualities. In fact, EPS leads the pack when it comes to R-value per dollar. This ratio of R-value to the total price of manufacturing and installation per sq. ft. of material is a crucial component of the process to deliver a budget-friendly, energy-efficient finished home or building. The manufacturing costs of EPS are generally lower compared to other materials, but when labor costs are factored in, EPS quickly surpasses other materials in R-value per dollar.
Given that this rigid foam insulation is easily installed, performs well against moisture below-grade and retains its R-value over time, builders, contractors, and architects frequently turn to EPS to not only save dollars but to fill a crucial need for most projects. With a myriad of product options available for rapid deployment, EPS insulation can offer project savings beyond the cost of production.
EPS is good for your overhead
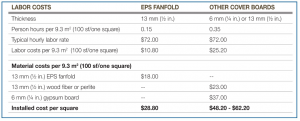
Some EPS products can help roofing contractors save up to 57% on labor costs.
In a roofing application, leading industry publication Construction Specifier calculated that, on average, a tapered EPS roofing system could save 22 percent in materials cost and more than 57 percent in labor costs when re-surfacing a roof compared to materials such as gypsum board. Additionally, EPS products available on today’s market offer cost savings in the form of reduced labor to move the lightweight material, less accessory materials and fasteners, as well as custom options to reduce the amount of field-cutting.
Continuous value in continuous insulation
EPS is one of the most versatile rigid insulations because it can be used anywhere in the building envelope – roof, walls or below-grade. As a rigid foam insulation manufacturer, Insulfoam offers a number of product options that help building teams reduce their continuous insulation labor and material costs.
For example, R-Tech Fanfold (FF), is made-up of 25 two-foot by four-foot faced EPS panels, with each panel attached to its neighbor along one side. The bundles weigh less than 11 pounds each, so it is easy for one person to carry two bundles instead of multiple people needing to carry the materials. And once the crew gets the panels where they need to be, the panels easily unfold to cover up to 200 square feet per bundle.
Go green while saving green
EPS insulation’s value is also realized in modern, environmentally-focused building projects. In commercial settings such as schools or hospitals, energy use and insulation can have a significant impact on many different aspects of construction costs, especially for roofing or below-grade uses. In a hospital, which is one of the most energy-consuming types of commercial buildings built today, EPS can be a cost-effective method to insulate the different surfaces of the building. Not only can EPS lower the cost of construction and lifetime cost of heating and cooling, but as building codes continue to push builders and architects to make these structures increasingly energy efficient, many EPS insulation products are ahead of those regulations.
Insulfoam manufactures its EPS solutions without any ozone-depleting agents, is often made of recycled material and is 100% recyclable if it ever needs to be replaced. In fact, Insulfoam EPS insulation can even qualify for LEED credits in certain applications.
Maintaining R-value per dollar is more than the cost of manufacturing the insulation you choose for your project. When architects and builders calculate the entire cost of a project, EPS quickly rises as one of the best options across all of the insulation needs. See how Insulfoam’s EPS products can save the budget of your next project.